引文格式:
Arakawa J ,Kawahara Y ,Kimura Y , et al. Estimation of the fatigue crack initiation site and life of Ti-6Al-4V alloy for two types of circle and slender crystal grains[J]. International Journal of Fatigue, 2024,181, 108097.
Jinta Arakawa, et al. "Estimation of the fatigue crack initiation site and life of Ti-6Al-4V alloy for two types of circle and slender crystal grains." International Journal of Fatigue 181 (2024): 108097.
Arakawa, J., Kawahara, Y., Kimura, Y., Hashimoto, S., Akebono, H., & Sugeta, A. (2024). Estimation of the fatigue crack initiation site and life of Ti-6Al-4V alloy for two types of circle and slender crystal grains. International Journal of Fatigue, 181, 108097.
背景简介
钛合金由于其具有优良的耐热性、耐腐蚀性、比强度和生物相容性,在许多工业领域得到了应用。特别是在飞机零件、人工髋关节等领域有着广泛的应用,且其需求还将不断增加。Ti-6Al-4V合金是由具有HCP(六方闭包体)结构的a相和具有HCP + BCC(体心立方)结构的a+b相组成的多晶体。这种合金的特点包括其优良的焊接性和由于热处理而产生的性能变化。到目前为止,许多报道表明,通过控制热处理条件可以改变材料的性能(如抗拉强度、屈服强度和韧性);但目前针对这种材料的疲劳裂纹萌生位置和寿命进行定量预测的例子很少。
因此,在本研究中,从晶体取向参数之一的晶粒形状入手,考虑晶粒形状为近乎完美的圆形或细长形状来确定滑移线长度。并尝试引入上述参数用于提高疲劳裂纹起裂位置预测的准确性。此外,通过试验获得了宏观疲劳裂纹萌生寿命,并利用施密特因子的晶粒尺寸和面外分量对宏观疲劳裂纹萌生寿命进行了统一评估。
成果介绍
(1)在细长晶粒出现疲劳裂纹的情况下,可以通过考虑施密特因子的平面外分量(SFsinΩ)来识别导致裂纹萌生的滑移系统。所有试样中的疲劳裂纹都是由初生a相的基体滑移引起的。下图显示了裂纹1和裂纹2分析的结果。
.png)
图1 疲劳裂纹1-1~裂纹2-1和SFsinΩ图
如图1所示,图A-2和图B-2显示了基于基体滑移得到的SFsinΩ。表3和表4中显示计算α角与试验裂纹萌生角一致,因此所有试样的疲劳裂纹萌生都是由于SFsinΩ较高的晶粒中发生来了基体滑移。
(2)关于疲劳裂纹萌生位置的预测,根据每个晶粒中促成裂纹萌生的基体滑移系统的滑移线长度与SFsinΩ之间的关系,不仅可以在圆形晶粒中估计疲劳裂纹萌生的候选晶粒,还可以在细长晶粒中估计疲劳裂纹萌生的候选晶粒。
在本研究中,我们绘制了具有两种晶粒形状的Ti-6Al-4V合金的(滑移线长度)-1/2和SFsinΩ关系图,并证实了它们之间的正相关性。因此,利用式(2),假设绘制在直线上方的晶粒是疲劳裂纹萌生的候选晶粒。结果如图2所示。该图显示了观察到裂纹3–2的试样的微观结构。如图2(a)所示,根据晶粒尺寸和SFsinΩ,我们可以将疲劳裂纹萌生位置的候选范围缩小到34.7 %。此外,如图2(b)所示,通过应用滑移线长度和SFsinΩ之间的关系,我们可以将疲劳裂纹萌生的候选晶粒数量限制在16.2 %。
.png)
图2 使用SFsinΩ、晶粒尺寸和滑移线长度定位疲劳裂纹萌生位置
(3)关于疲劳裂纹萌生时间的预测,宏观疲劳裂纹萌生时间可以使用结合了微观裂纹萌生驱动力Pi和微观裂纹扩展驱动力Pp的参数P来估计。
式(1)和(2)是通过考虑裂纹萌生处晶粒的滑移线长度In与微裂纹引发和微裂纹扩展的驱动力来计算的。此外,如果基于考虑Pi和Pp的对数-对数线性回归模型的疲劳寿命曲线,则宏观裂纹萌生时间N可表示为式(3)。这里,A和B是常数,a(0≦a≦1.0)表示Pi对总驱动力P的贡献率。当公式最终转换时,它表示为式(5)。总驱动力P和宏观裂纹萌生寿命N之间的关系变为式(6)。
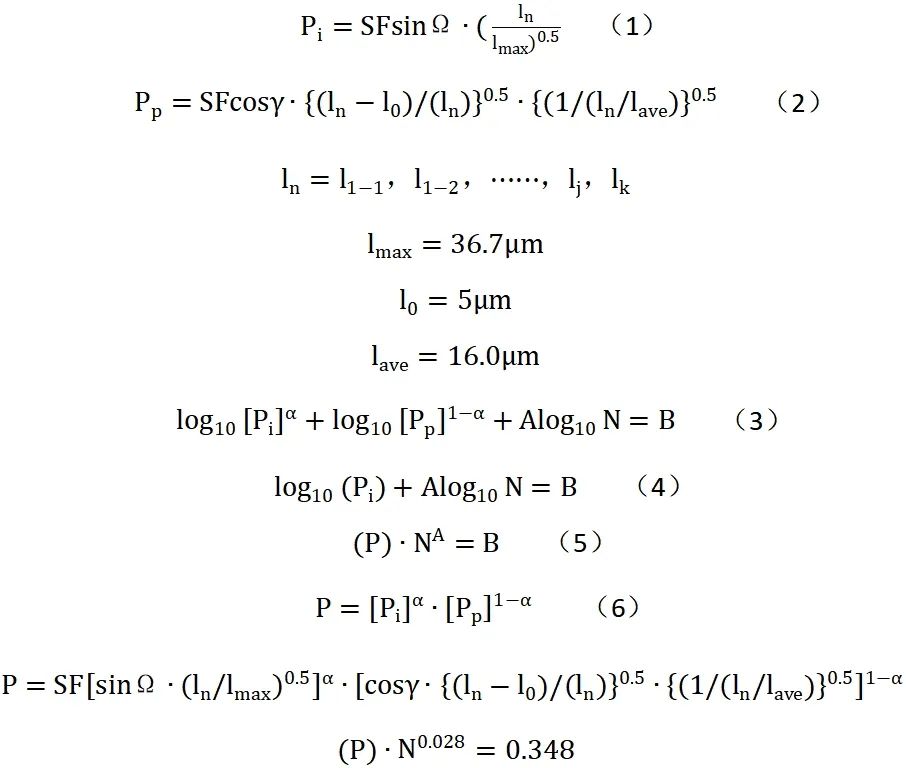
图3是每个贡献率a的P-N曲线的相关系数r和标准偏差σ的变化图。在该图中,纵轴是r,1-σ,横轴是a的值。换句话说,当函数 f1 - f2最大时,疲劳寿命曲线表现出高相关性r和小变化σ。基于计算出的a为0.58,给出相应的疲劳寿命的P-N曲线如图4所示。从图中观察到,宏观裂纹萌生寿命N可以通过驱动力P精确预测,并且可以使用该评估方法来估计宏观疲劳裂纹萌生时间。
.png)
图3 1-σ,r与贡献率a的关系
.png)
图4 a= 0.58下N和P之间的关系
本文通讯作者:Hiroyuki Akebono(Department of the Mechanical Science and Engineering, Graduate School of Engineering, Hiroshima University, 1-4-1 Kagamiyama, Higashi-Hiroshima, Hiroshima 739-8527, Japan)。
本期小编:刘尧风(整理)
闵 琳(校对)
舒 阳(审核)
王永杰(发布)
|