引文格式:
Falkowska A, Tomczyk A, Seweryn A. The effect of elevated temperature on LCF damage growth in 2024AA-Experiment and modeling [J]. Engineering Failure Analysis, 2024, 158: 108015.
Falkowska A, et al. "The effect of elevated temperature on LCF damage growth in 2024AA-Experiment and modeling." Engineering Failure Analysis 158 (2024): 108015.
Falkowska A., Tomczyk A., & Seweryn A. (2024). The effect of elevated temperature on LCF damage growth in 2024AA-Experiment and modeling. Engineering Failure Analysis, 158, 108015.
背景简介
几十年来,铝合金由于具有良好的耐腐蚀性、良好的强度重量比、高导电性和导热性,因此被广泛应用于许多行业,例如飞机工业、汽车或造船业。许多由铝合金制成的结构元件在疲劳载荷状态下在较宽的温度范围内运行。发动机气缸盖的工作温度最高可达250℃,重型车辆的增压空气冷却器最高可达275℃,发动机气缸活塞面甚至可以达到400℃以上。在飞机工业中,铝合金常用于机身框架、机翼纵梁、机翼蒙皮和各种连接件。在使用寿命条件下,这些元件可能会在非常低的温度下承受疲劳载荷,甚至低至-60℃。在超声波以高于2马赫的速度飞行的情况下,温度可以达到120℃。因此,铝合金在高温下的疲劳问题仍然很重要。
试验方案
使用 EN-AW2024铝合金在T3511回火中进行了试验。该合金的化学成分如表1所示。使用加工(车削)技术制造螺纹直径为 16 毫米的试样,该试样标距段直径为 6.5 mm、标距长度为 13 mm (图1)。
表1 2024AA合金的化学成分

.png)
图1 疲劳试验中试样尺寸示意图
测试在100℃,200℃和300℃的高温下进行。每个温度下的加热速率为100℃时为3℃/min,200℃时为5℃/min,300℃时为8℃/min。达到设定温度后,将样品在这些条件下保持5分钟,以保证试整个试样温度恒定。
图2给出了不同温度下的试验循环应力-应变曲线及近似值,从图中可以看出该材料在室温和100℃下的行为在塑性应变和应力方面没有显示出明显差异。
.png)
图2 室温和高温下的循环应力-应变曲线
成果介绍
(1)从图3中可以看出当εa=0.005时,塑性应变非常小,环路呈现为一条直线。此外,在任意应变幅值条件下,温度为20℃、100℃和200℃时,滞回曲线几乎一致而在300℃的条件下观察到了不同的滞回曲线。
.png)
图3 不同温度下应变幅值εa (a) 0.008,(b) 0.005,(c)0.01,(d)0.015,(e)0.02对应的稳定滞回曲线
(2)从图4中可以看出,在300℃的温度下,断裂面与低温下的疲劳类型一致,这是由于在循环的最后阶段,样品断裂过程中产生了较高的塑性应变导致疲劳破环平面的方向垂直于载荷方向。在100℃和200℃时,该平面通常与载荷方向成约45°的角度。
.png)
图4 εa=0.005和εa=0.02的LCF断面方向:a)100℃;b)200℃;c)300℃
(3)SEM断口形貌如图5所示,在100℃时断口上有一个垂直于加载方面的较小的中心,外部较大区域相对于垂直加载面方向倾斜约45℃。中心区域较为粗糙,产生这种变形的主要原因是最大主应力。此外在孔隙底部观察到许多粗沉淀物,通常是裂纹萌生的原因。如图6所示,与100℃相似,在200℃时疲劳断裂形貌也表明最大主应力起主导作用,较高的温度导致孔隙残余物比较低的温度更深。这主要与材料在高温下保持的时间明显更长有关,因此,微观结构变化发生的可能性更大。同时,可以观察到较小的相邻孔隙合并的明显趋势。在小应变的情况下,这种合并通常发生在位于样品不同高度的材料的相邻部分。如图7所示,300℃时,较小孔隙相互融合,尤其在小应变情况下。在高放大倍率下,可以看到较小孔隙簇的残余物,这些孔隙由于合并而形成较大的孔隙,具有相当大的深度和直径。横截面的边缘,即其靠近样品表面的外部部分,被一个不同性质的区域所占据,最初沿样品轴方向拉伸的孔隙最终由于切向应力的作用而被破坏,其在大应变下更为明显。
.png)
图5 100℃下SEM断口形貌:a) εa=0.005;b) εa=0.02;c) 断口中心
.png)
图6 200℃下SEM断口形貌:a) εa=0.005; b) εa=0.02; c) 断口中心
.png)
图7 300℃下SEM断口形貌:a) εa=0.005;b) εa=0.02;c) 断口中心;d) 断口边缘
(4)疲劳损伤建模:
假设损伤主要是由于主应力的作用累积的,且损伤主要由塑性应变和法向应力的增加而增加,其增量表示为单轴载荷条件:
.jpg)
σ-实际额定应力, σu-极限拉应力,Aw、nw-与温度相关的材料参数。未损伤时w=0,断裂时w=1。它们在单个循环中的增量可以表示为等温条件:
.jpg)
其中wb、we-加载循环中损伤变量w的初始值和最终值。积分后可获得能量w与εap间的关系:
.jpg)
可将上面的等式用更简单的形式写成:
.jpg)
假设每个周期中损坏程度相同:
.jpg)
上式可简化为:
.jpg)
其中:
.jpg)
参数Aw、nw 可定义为:
.jpg)
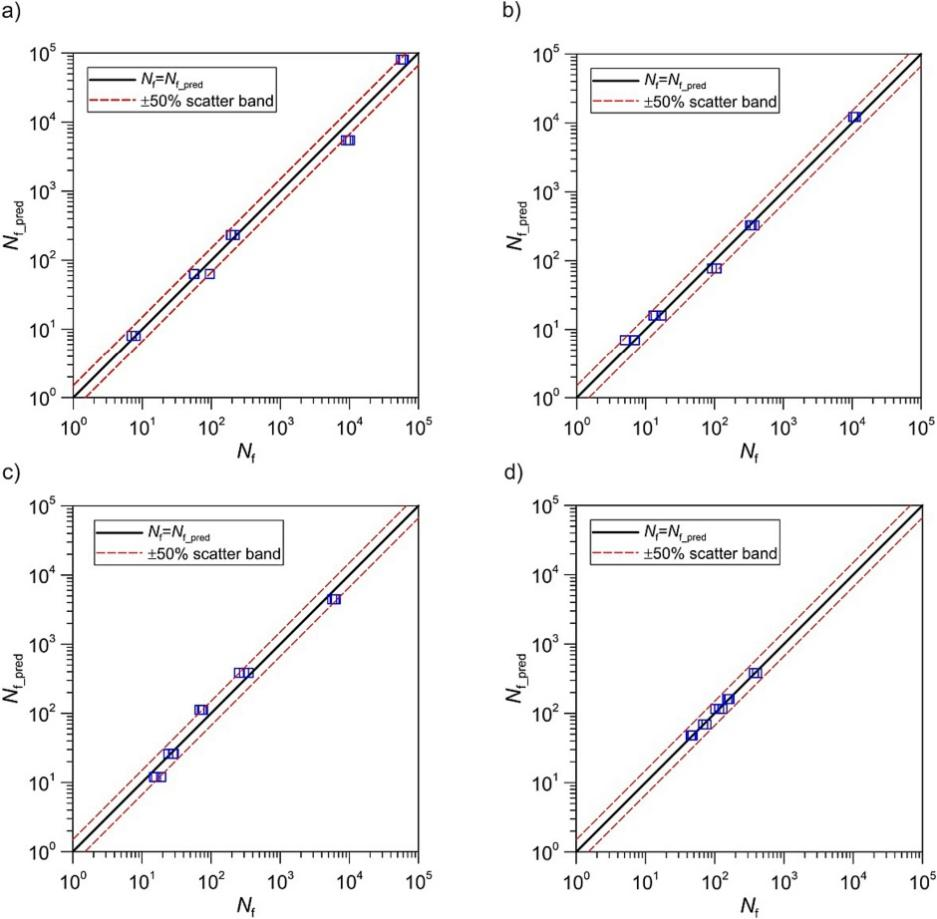
图8 不同应变幅下的预测寿命:(a) 20℃;(b) 100℃;(c) 200℃;(d) 300℃
图8中可以看出,通过本文提出的方法在不同温度和不同应变幅预测的疲劳寿命都位于2倍分散带内,取得了良好的预测效果。
本文通讯作者:Adam Tomczyk (Białystok University of Technology, Faculty of Mechanical Engineering, Wiejska 45C Str., 15-351 Białystok, Poland)。
本期小编:华飞龙(整理)
闵 琳(校对)
舒 阳(审核)
王永杰(发布)
|